Live Edge Now 50% off!
20 Live Edge Pieces Remaining with
40 more Arriving in the next Two Weeks!
Retail of $6,487 for 50% off
Hard Maple Live Edge at 50% off|
HM2
Species : Hard Maple
Thickness : 1.5
Avg Width : 12.33
Length : 10
Total : $243
Now 50% off $121.50
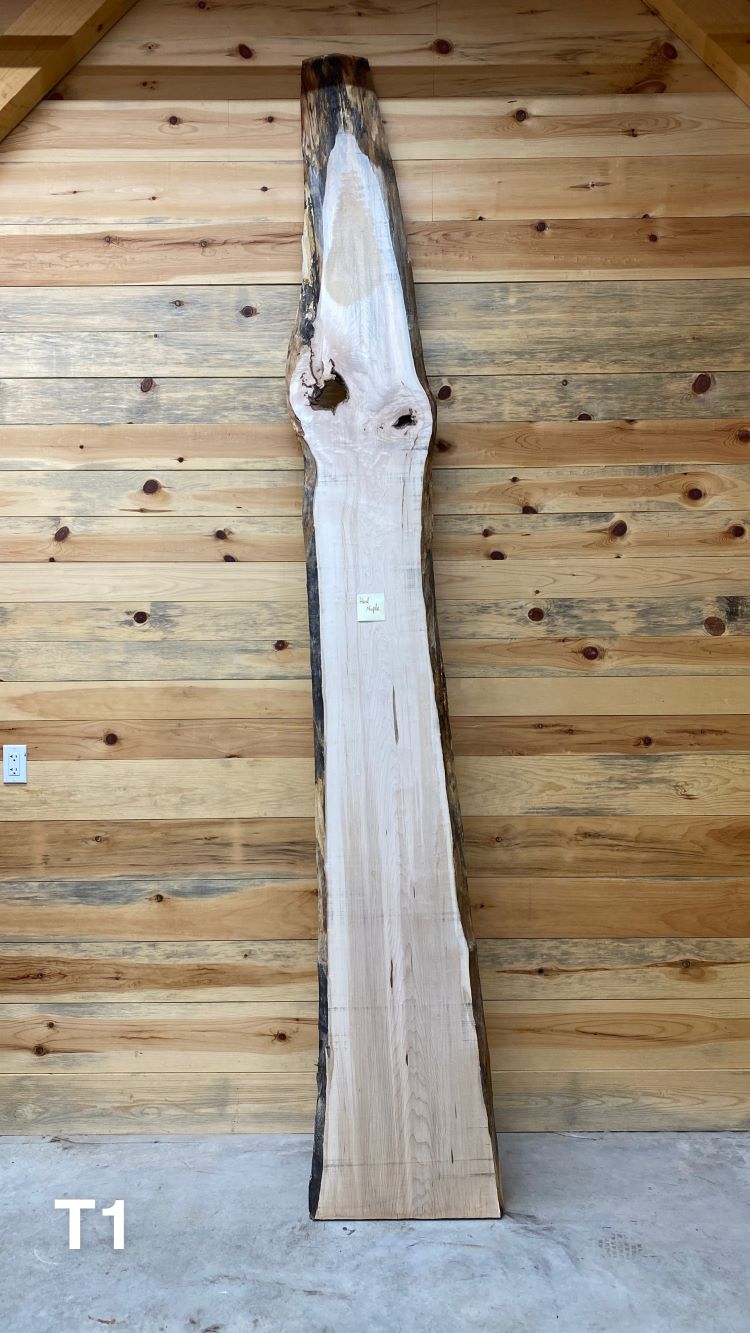
HM13
Species : Hard Maple
Thickness : 1.75″
Avg Width : 11.33″
Length : 10′
Total : $259.17
Now 50% off $129.59
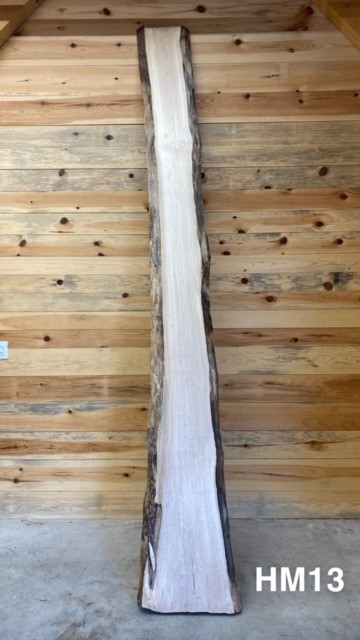
HM10
Species : Hard Maple
Thickness : 1.75″
Avg Width : 12.67″
Length : 10′
Total : $289.83
Now 50% off $144.91
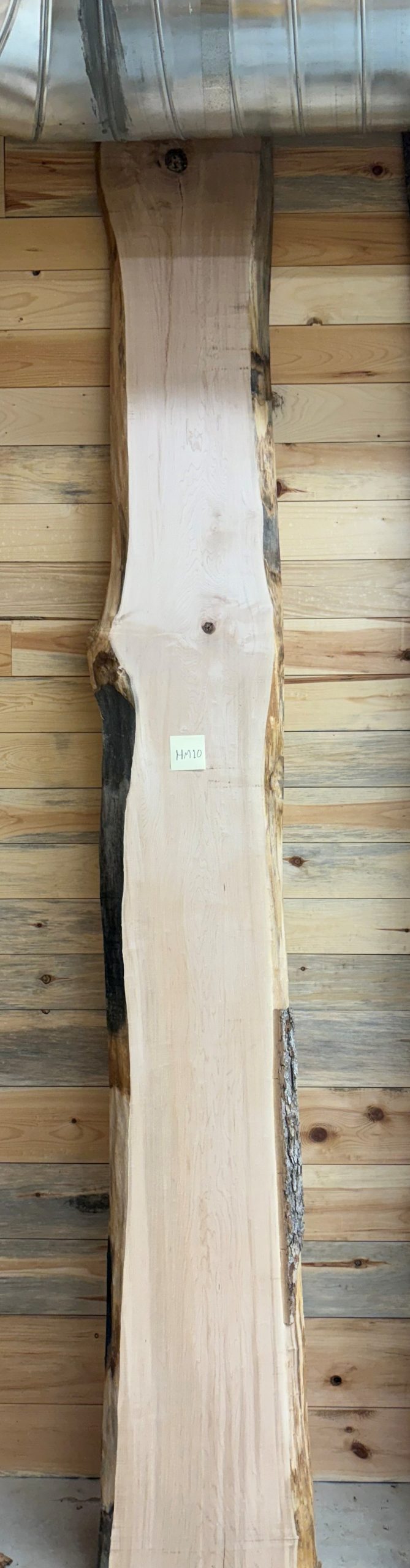
HM11
Species : Hard Maple
Thickness : 1.75″
Avg Width : 15″
Length : 10′
Total : $343.13
Now 50% off $171.56
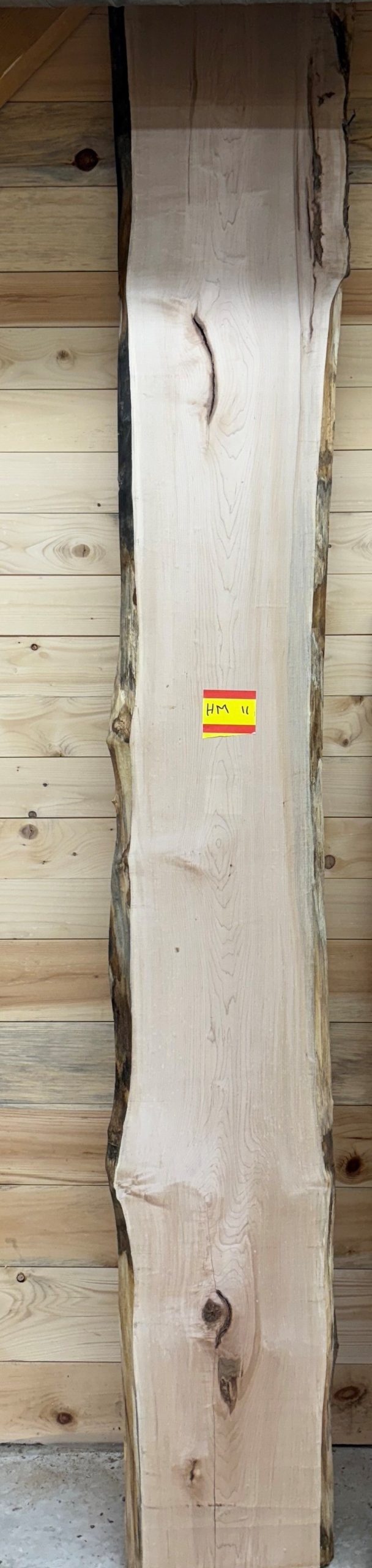
HM25
Species : Hard Maple
Thickness : 1.50″
Avg Width : 20″
Length : 10′
Total : $394.17
Now 50% off $197.08

HM37
Species : Hard Maple
Thickness : 1.00″
Avg Width : 13.0″
Length : 6′
Total : $115.29
Now 50% off $57.65

HM38 Sold
Species : Hard Maple
Thickness : 1.0″
Avg Width : 13″
Length : 6′
Total : $115.29
Now 50% off $57.65 Sold

HM36
Species : Hard Maple
Thickness : 2.0″
Avg Width : 13″
Length : 4′
Total : $136.23
Now 50% off $68.12
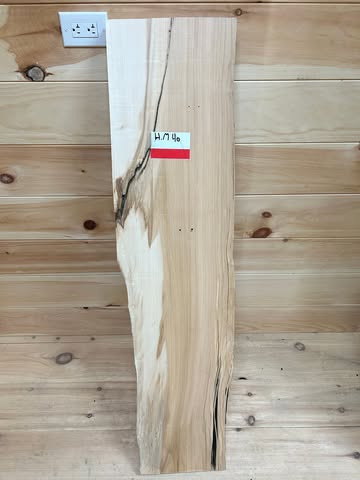
HM39
Species : Hard Maple
Thickness : 1.5″
Avg Width : 13.5″
Length : 9′
Total : $274.93
Now 50% off $137.47
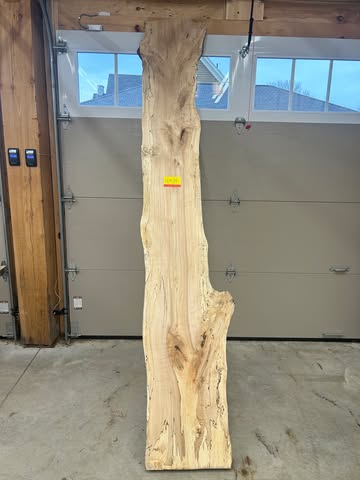
HM40
Species : Hard Maple
Thickness : 2.0″
Avg Width : 15.5″
Length : 9′
Total : $365.43
Now 50% off $182.71
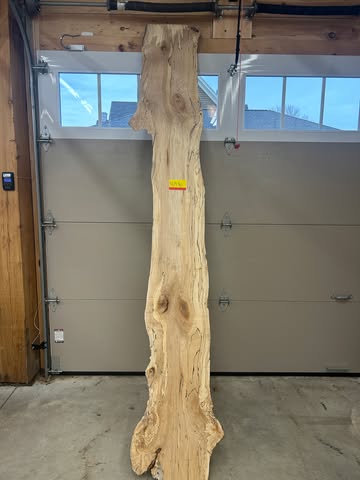
HM41 "Sold"
Species : Hard Maple
Thickness : 1.5″
Avg Width : 13.0″
Length : 12′
Total : $307.45
Now 50% off $153.73 “Sold”
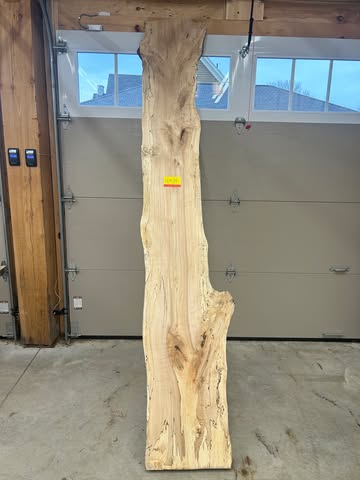
HM42
Species : Hard Maple
Thickness : 1.5″
Avg Width : 15.0″
Length : 12′
Total : $354.46
Now 50% off $177.38
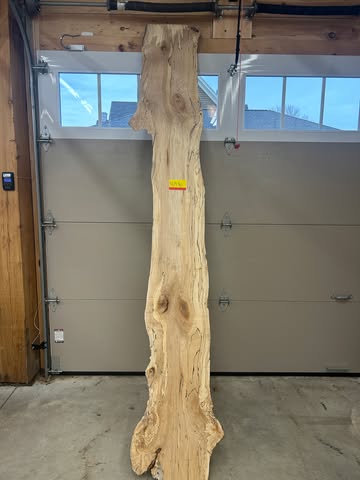
HM43
Species : Hard Maple
Thickness : 1.5″
Avg Width : 14.5″
Length : 6′
Total : $171.47
Now 50% off $85.73

HM44
Species : Hard Maple
Thickness : 1.5″
Avg Width : 16.5″
Length : 9′
Total : $292.67
Now 50% off $146.33
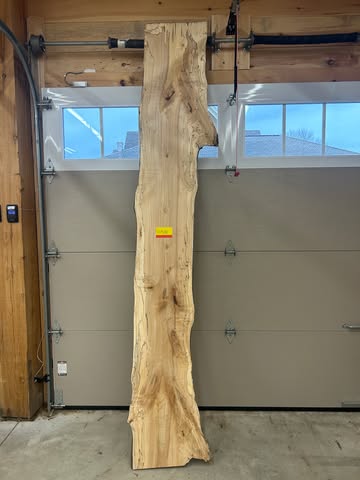
HM45
Species : Hard Maple
Thickness : 1.25″
Avg Width : 15.0″
Length : 8′
Total : $200.38
Now 50% off $100.19
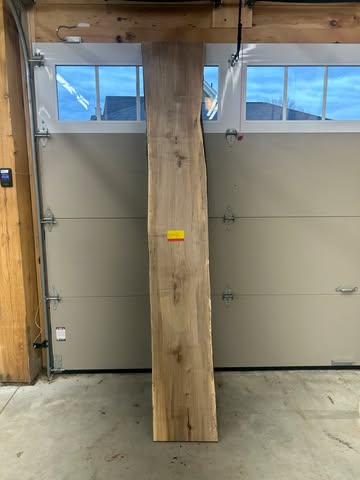
HM46
Species : Hard Maple
Thickness : 1.25″
Avg Width : 19.5″
Length : 9′
Total : $293.01
Now 50% off $146.50
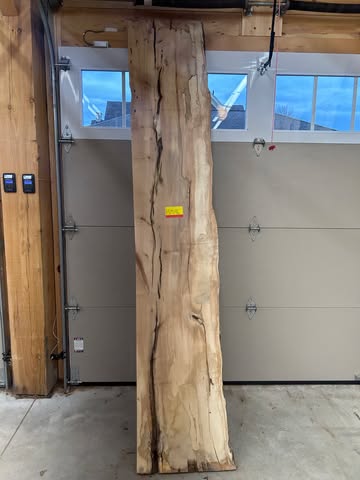
HM47
Species : Hard Maple
Thickness : 1.5″
Avg Width : 17.50″
Length : 9′
Total : $310.52
Now 50% off $155.26
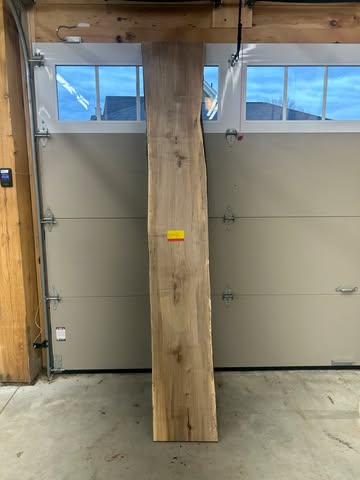
HM48
Species : Hard Maple
Thickness : 1.5″
Avg Width : 19.0″
Length : 9′
Total : $337.01
Now 50% off $168.51
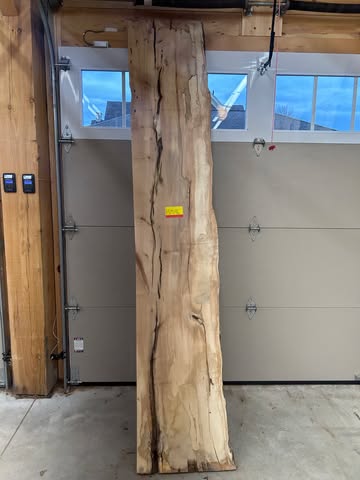
HM50
Species : Hard Maple
Thickness : 1.5″
Avg Width : 18.5″
Length : 9′
Total : $328.14
Now 50% off $164.07
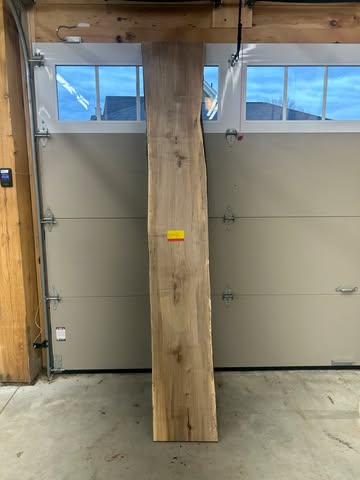
HM51
Species : Hard Maple
Thickness : 1.25″
Avg Width : 18.5″
Length : 9′
Total : $278.25
Now 50% off $139.12
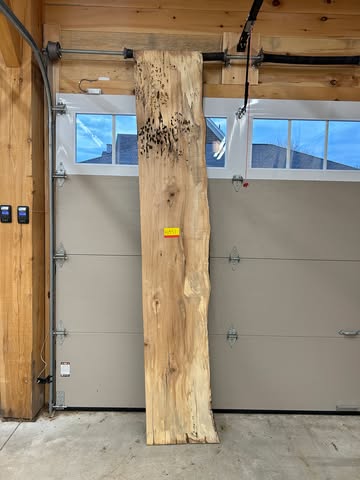
Soft Maple & Cherry Live Edge at 50% off
Cherry Square CH 7
Species : Cherry
Thickness : 1.25″
Avg Width : 11″
Length : 8′
Total : $100.74
Now 50% off $50.37
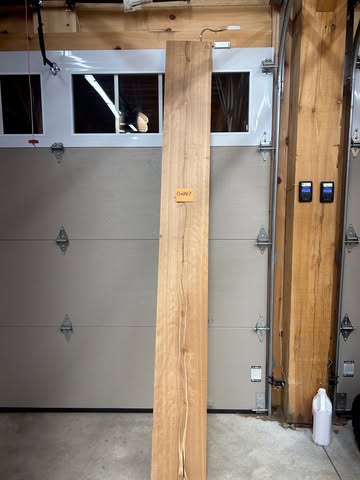
SM7
Species : Soft Maple
Thickness : 1.75
Avg Width : 13.5
Length : 8
Total : $205.03
Now 50% off $102.52
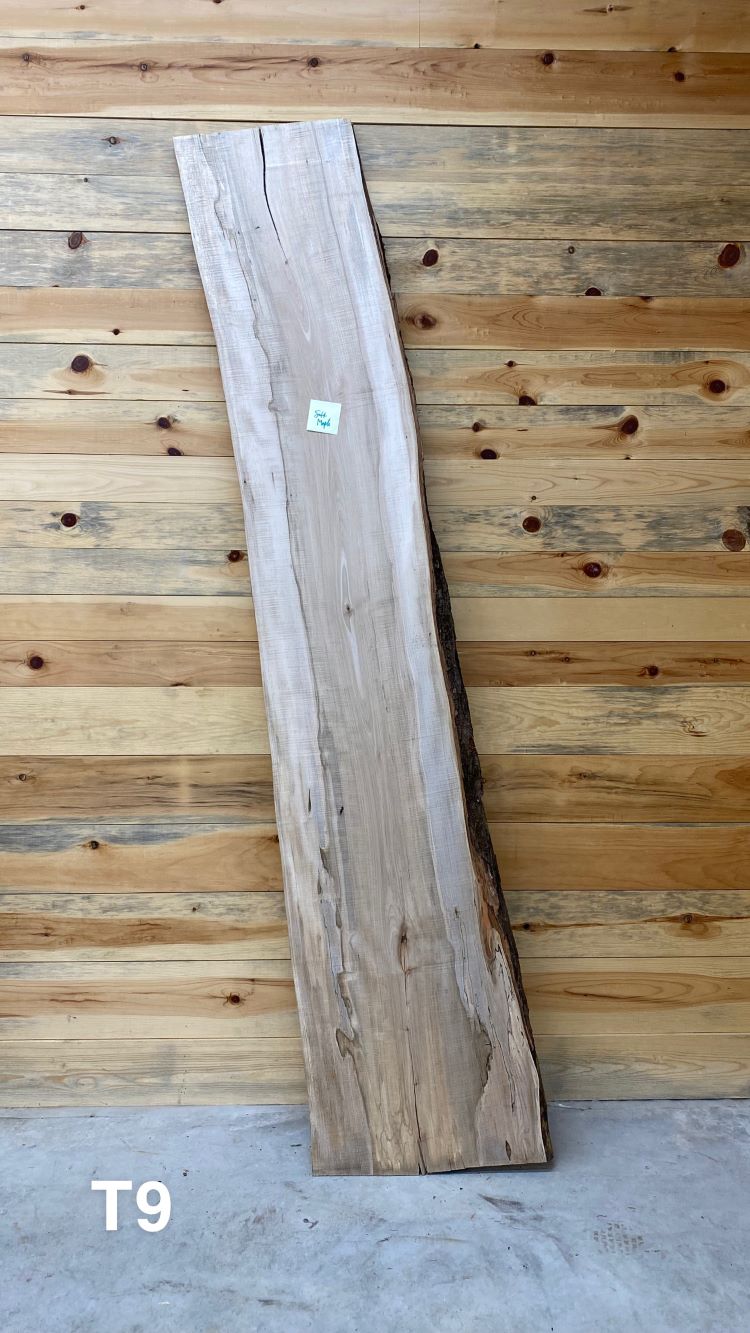
SM 8
Species : Soft Maple
Thickness : 1.25″
Avg Width : 14″
Length : 8′
Total : $186.98
Now 50% off $93.49
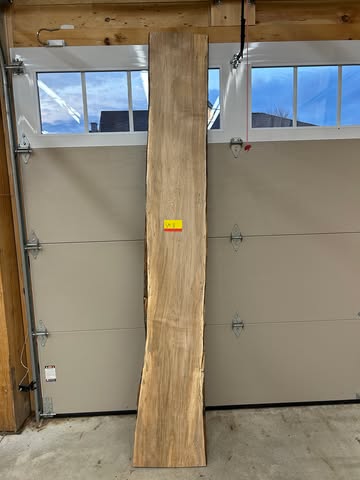
SM 9
Species : Soft Maple
Thickness : 1.5
Avg Width : 13.0
Length : 10
Total : $256.25
Now 50% off $128.12
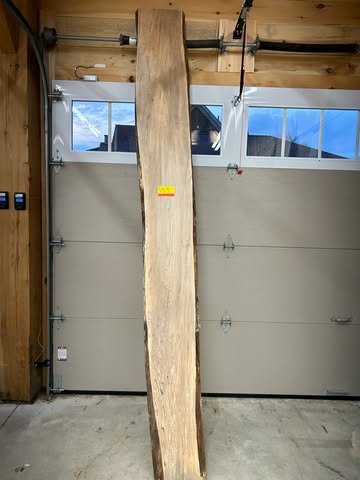
SM 10
Species : Soft Maple
Thickness : 1.5″
Avg Width : 14.5″
Length : 8′
Total : $228.58
Now 50% off $114.29
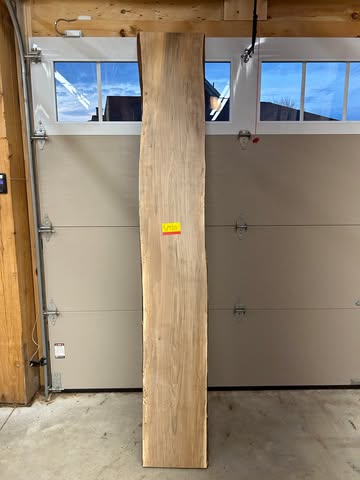
SM 11
Species : Soft Maple
Thickness : 1.0
Avg Width : 12.5
Length : 8
Total : $129.06
Now 50% off $64.53
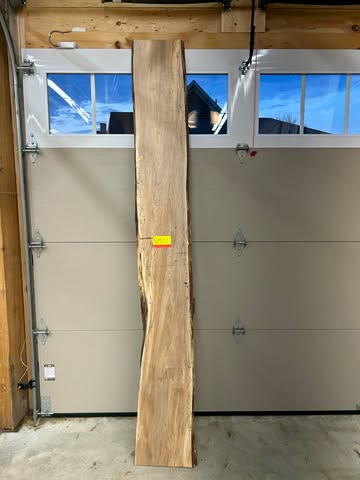
White & Red Oak Square Edge & Two Red Oak Live Edge at 50% off
WO18 Square
Species : White Oak
Thickness : 1.5
Avg Width : 12″
Length : 2
Total : $58.45
Now 50% off $29.23
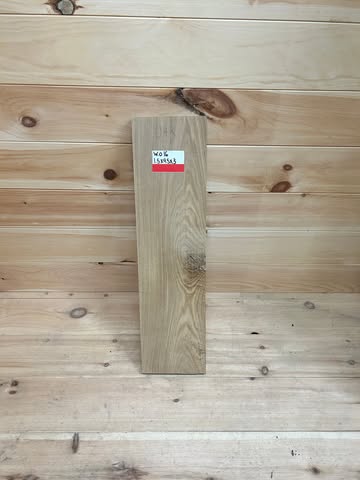
WO19 Square
Species : White Oak
Thickness : 1.5
Avg Width : 12
Length : 2
Total : $58.45
Now 50% off $29.23
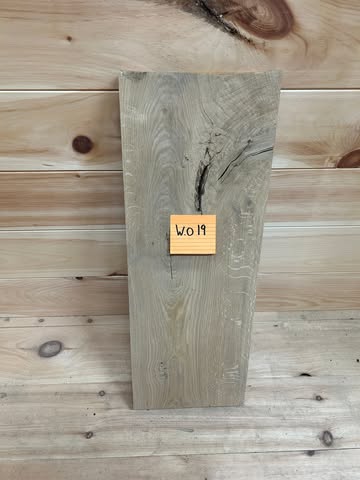
WO20 Square
Species : White Oak
Thickness : 1.5
Avg Width : 10.5
Length : 1.5
Total : $38.36
Now 50% off $19.18
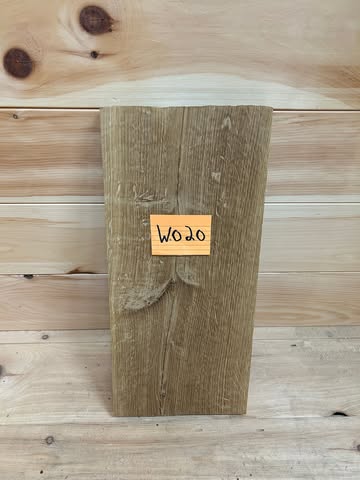
Red Oak 1
Species : Red Oak
Thickness : 0.75
Avg Width : 13.75
Length : 7
Total : $88.46
Now 50% off $44.23

Red Oak 2 Square
Species : Red Oak
Thickness : 1.5
Avg Width : 10.0
Length : 4
Total : $61.03
Now 50% off $30.52
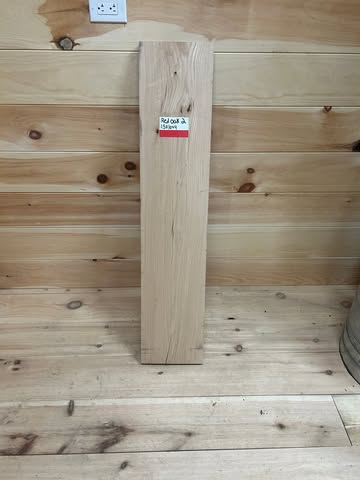
Red Oak 3 Square
Species : Red Oak
Thickness : 1.5
Avg Width : 10.0
Length : 4
Total : $61.03
Now 50% off $30.52
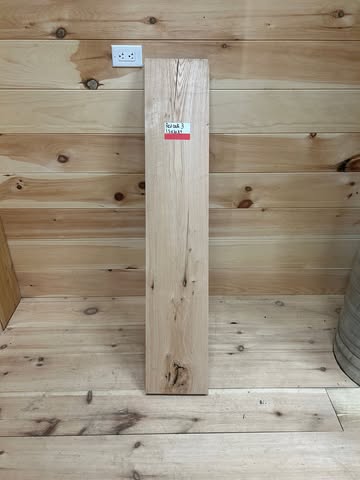
Red Oak 4 Square
Species : Red Oak
Thickness : 1.5
Avg Width : 6.75
Length : 3
Total : $31.00
Now 50% off $15.50
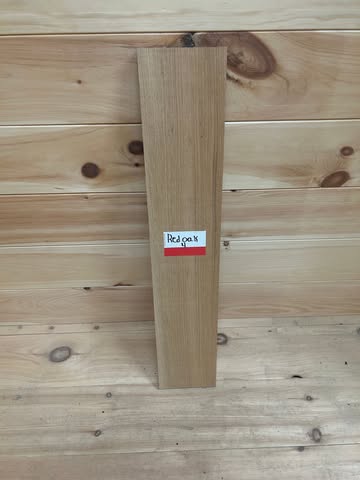
Red Oak 6 Square Sold
Species : Red Oak
Thickness : .875
Avg Width : 13
Length : 10
Total : $117.21
Now 50% off $58.61 Sold
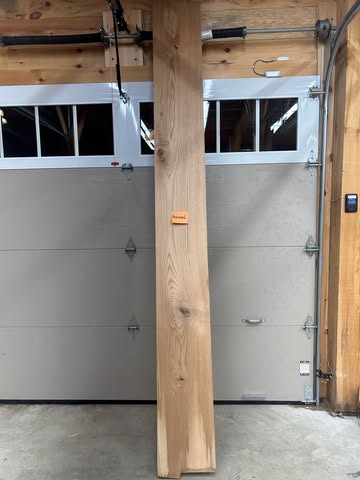
Red Oak 07
Species : Red Oak
Thickness : 2.0
Avg Width : 20″
Length : 8′
Total : $419.12
Now 50% off $209.56

Red Oak 08
Species : Red Oak
Thickness :2.0
Avg Width : 18.5
Length : 8
Total : $282.43
Now 50% off $193.21
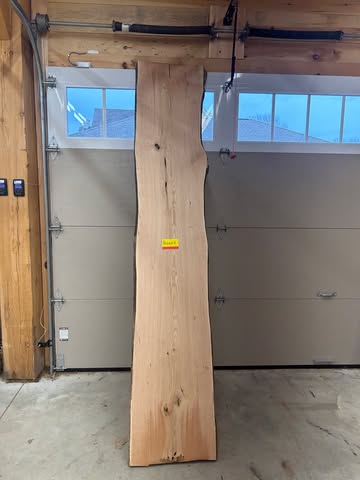
Red Oak 9
Species : Red Oak
Thickness : 2.0
Avg Width : 17″
Length : 8′
Total : $240.47
Now 50% off $140.23
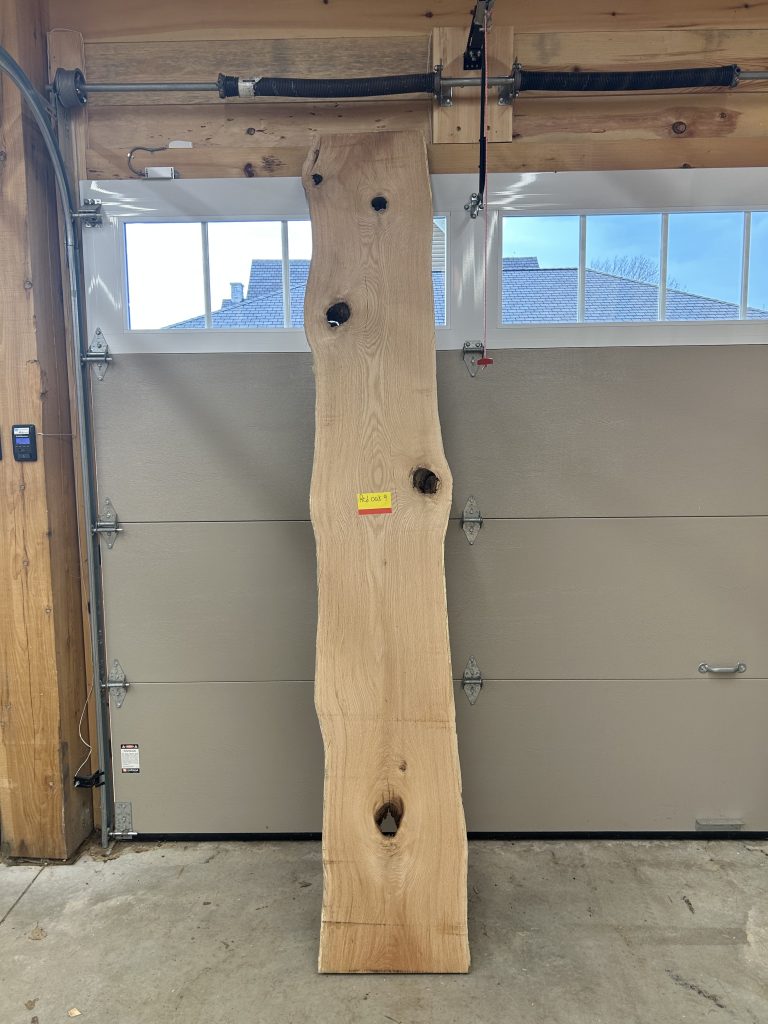
Red Oak 10
Species : Red Oak
Thickness :2.0
Avg Width : 15
Length : 8
Total : $247.50
Now 50% off $123.75
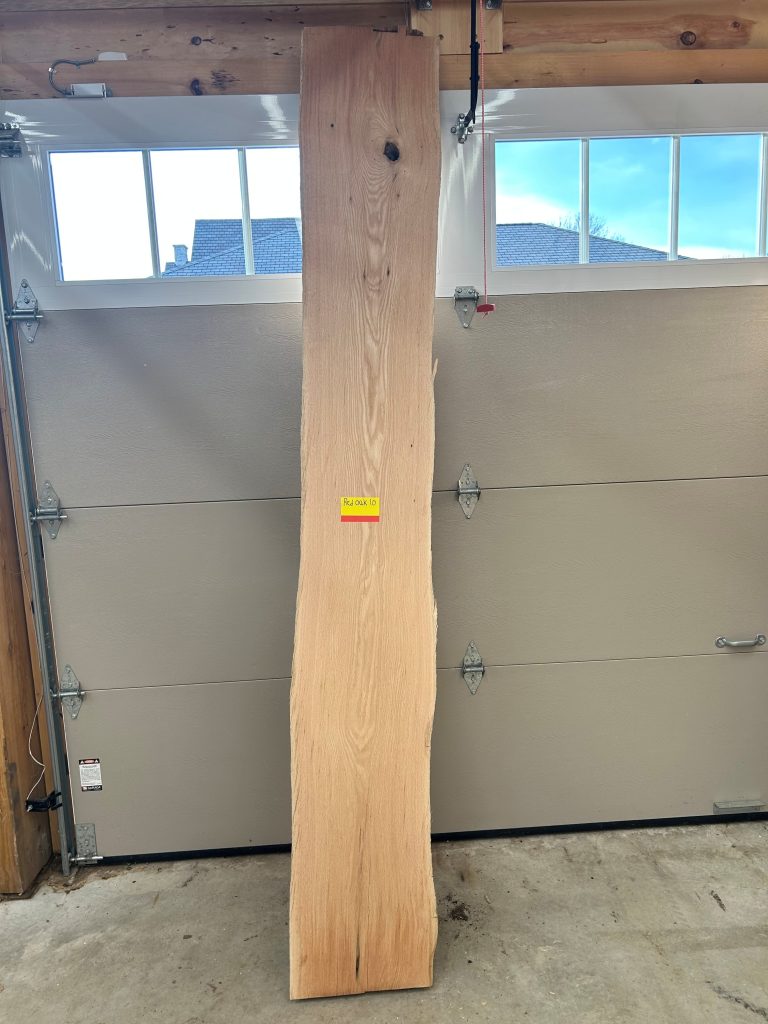
Red Oak 11
Species : Red Oak
Thickness : 1.5
Avg Width : 19.5″
Length : 8′
Total : $237.90
Now 50% off $118.95


Red Oak 12
Species : Red Oak
Thickness :1.5
Avg Width : 18.5
Length : 8
Total : $225.73
Now 50% off $112.87
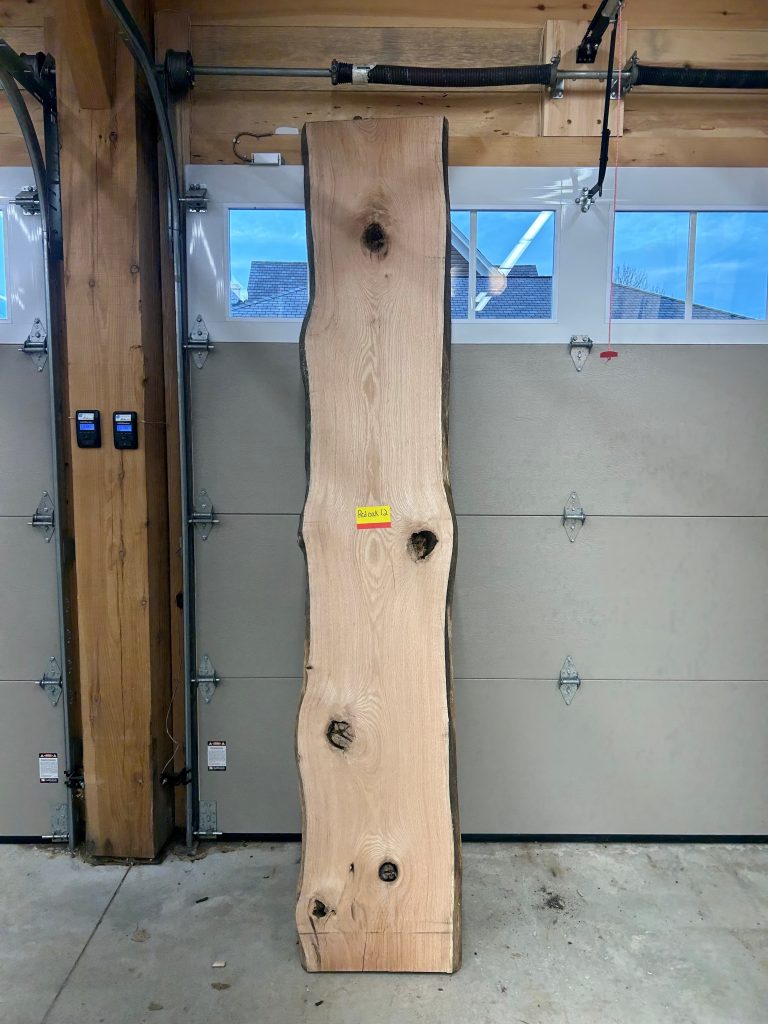
Red Oak 13
Species : Red Oak
Thickness : 2.0
Avg Width : 18.0″
Length : 8′
Total : $297.00
Now 50% off $148.50
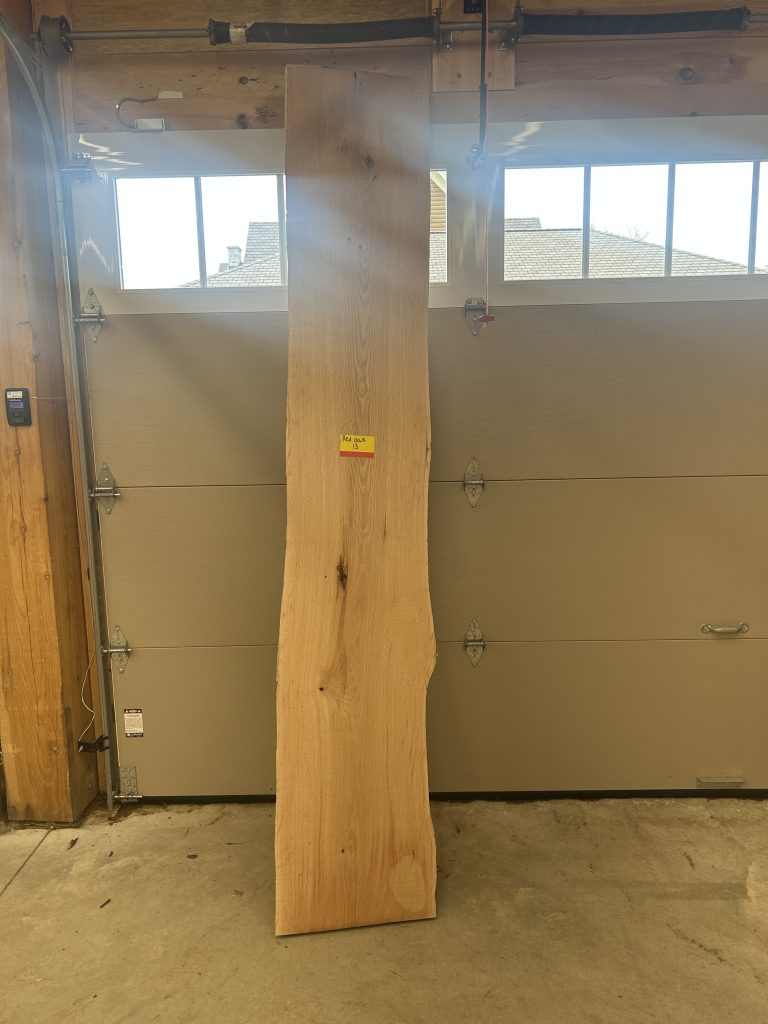
White Ash Square Edge at 50% off
AS25
Species : White Ash
Thickness : 2
Avg Width :19.5
Length : 1.5
Total : $53.87
Now 50% off $26.93
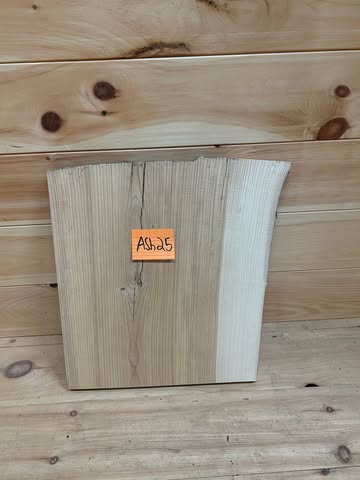
AS26
Species : White Ash
Thickness : 1.5
Avg Width : 15.5
Length : 1.5
Total : $39.91
Now 50% off $19.96
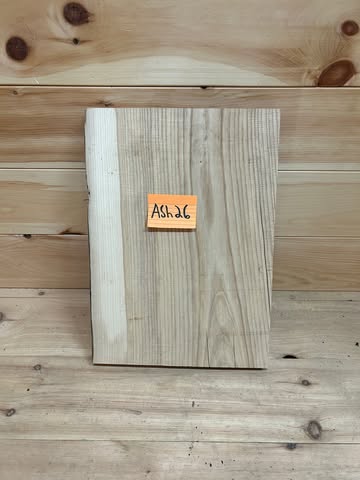
Extra Value as Air Dried to Only 17 to 20%
Outdoor Use
ADHM 1
ADAS 1
Species : Hard Maple
Thickness : 1.25″
Avg Width :14″
Length : 12′
Total : $216.21
Now 50% off $108.11
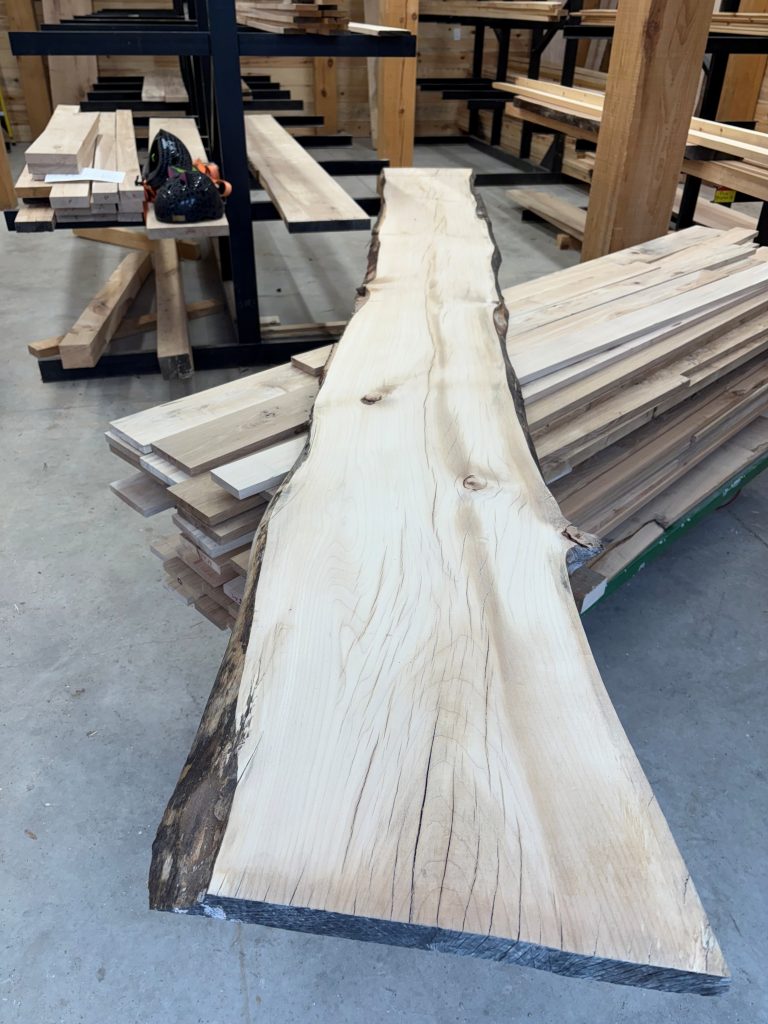
Species : White Ash
Thickness : 1.75″
Avg Width :12″
Length : 10′
Total : $164.69
Now 50% off $81.84
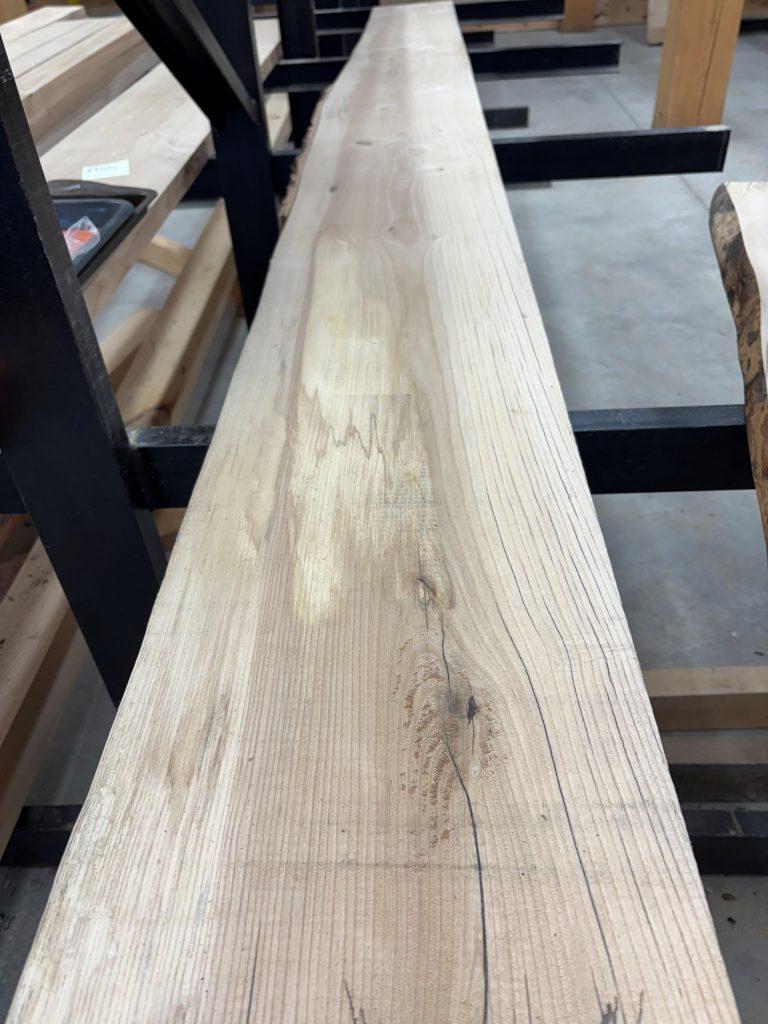